8 years, 7 months ago
#MakerMonday with Field Ready
We spoke to Laura James, Co-Founder of Field Ready, about how her team are not only building the things disaster areas need, but also empowering people across the globe with technology and skills they need to respond to a crisis.
What if we could make things immediately where and when they are needed, like in refugee camps or hospitals, instead of relying on unpredictable donations, supply chains and shipping? What if a vital water pipe broke and you could fix it within an hour by printing a replacement part for very little expense? Non-profit startup Field Ready aren’t just playing with these ideas, they are, as the name suggests, out in the field making, empowering and helping people save lives in countries hit by disaster using the technology of the maker movement, like 3D printing, to make sure people have what they need, when they need it. We chatted to Co-Founder Laura, an engineer by training with a very varied background in different cutting edge technologies and organisations, about how innovation is changing the way we respond to disasters.
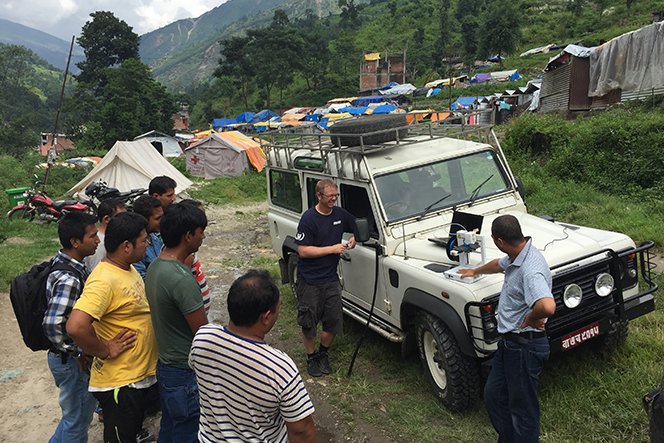
Q: Tell us about Field Ready.
A: Field Ready is a non-profit, which is transforming humanitarian aid supply chains to deliver items more efficiently and effectively to people in need. We show that it’s possible to manufacture supplies in the field so people can get the items they need most, when and where they need them. We do this mostly through digital manufacturing, such as 3D printing, and we use the internet to share designs, training materials, and to connect folks to help each other.
Q: What led you to Field Ready?
A: Serendipity - meeting the right people at the right moment - and then the appeal of the opportunity! Engineering has the power to change the world and I try to use my skills to help people, at the biggest scale possible. Field Ready is creating new ways to help people in their greatest need, after natural disasters, in refugee camps and other humanitarian crises. It’s not an easy problem, but the complex challenges are worth the effort.
Q: What kind of projects have you worked on? A: I started out helping with communications and fundraising and more recently I’ve represented Field Ready at the Singularity University Accelerator, where we worked on strategy with the help of great mentors and coaches. Q: What kind of new technologies do you use in Field Ready? A: We choose technologies pragmatically, but ultimately our vision is possible because of digital manufacturing, where an item can be made by a machine to a computerised design - that means that it’s easier for folks to make whatever they need with some common machinery. The first manufacturing technology we focussed on was 3D printing. We used this to make medical disposable items, like umbilical cord clamps, oxygen tube splitters and so on, in Haiti. We’ve also made replacement parts for high value assets which have broken - for instance, baby warmers lying unused in storage in a hospital in Nepal. These had broken corners, leaving jagged edges and repairs with tape just weren’t good enough. The warmers were second hand, donated, and you couldn’t get spare parts anywhere in the world, let alone after the quake in Nepal, because they were obsolete. However, we were able to design and 3D print new corners, stronger than the original ones so they wouldn’t break - resurrecting the baby warmers - expensive items which would not be replaceable. So 3D printing is very versatile. In Nepal, we made a pipe connector to help join together random bits of pipe supplying water to families living in camps after the quake. Pipes are just strung over the mountainside and may supply dozens of families. When we revisited six months later the connector was still in place, working well, no leaks, and no sign of environmental damage. So we’ve worked with a team of students at Imperial College to create our first app, which takes the sizes of pipes you need to join, and automatically generates a 3D model of the connector you need, ready to print. That way you can join any two pipes in the field very quickly without needing any 3D design skills.
We’re now looking at other techniques such as portable injection moulders, new ways of turning plastic waste into useful items like insulation blankets, and more.
Q: How has new tech, eg. desktop 3D printers, changed the way we can respond to emergencies?
A: The traditional way of supplying aid is to guess what supplies are going to be needed in an area in emergency, and find them in a warehouse somewhere in the world, and then ship them to where you need them. This is expensive, about 60-80% of the aid budget goes on logistics (warehousing, procurement, transport and so on) and despite this, many people in the aftermath of crises won’t get supplies they need for months or even years. Supplies also stop arriving in longer duration crises; two years after the quake in Haiti new supplies weren’t coming in and we visited a clinic which had basically run out of sterile items. The disaster wasn’t news any more and donations weren’t coming in.
By making supplies in the field, using general purpose manufacturing techniques like 3D printing, an affected community can make whatever they need most. Instead of shipping in a bunch of supplies that may not be what is needed, we take a machine and materials in, so that immediate needs can be met, and there’s ongoing capability to make more items or other items as needed.
Q: If you had to pick one piece of tech to take with you into an unknown situation, what would it be & why?
A: Oh, tough question, but I don’t know that I’d take a piece of tech. I’d rather take a capable person!
Challenging situations of the kind we meet in the field have so many facets - social, economic, cultural, as well as technical.
Q: Why’s it so important that humanitarian and innovation led projects work together?
A: We need humanitarian expertise that helps us work appropriately, respectfully and safely in context, and technology expertise that can see the potential of digital technologies and make them work, even in technically challenging settings. Both technologies, and humanitarian contexts, are complex, so you need both lots of understanding.
We also work with great designers and ethnographers, who can help us identify key needs on the ground and work with communities to solve problems in ways appropriate for them.
Q: How do you think we can bridge the gap?
A: I don’t know that I’d frame it as a gap. Like many projects, it’s just about finding ways for people from different backgrounds and with very different skills to communicate and collaborate effectively. That’s partly about finding collaborative people, partly support and training, partly using the right tools.
Q: What’s your personal favourite project with Field Ready?
A: One of our best examples of the power of 3D printing is how we can resurrect high value assets by fixing them up - the baby warmers in Nepal for instance. That’s really powerful, not just adding the value of a small plastic consumable/disposable part, but unlocking the value of something rare and important too.
Q: What’s the dream going forward?
A: We want to see local communities empowered to take control of their situations, able to access all the supplies they need in a timely fashion after disasters or other crises. We want local groups to be prepared for disasters with local robust manufacturing infrastructure which can be used to meet needs when needed. This should be supported by robust manufacturing equipment, open source hardware which is repairable and maintainable in the field. Also, a catalog of shared designs for all sorts of humanitarian items, which are easy to make in the field, using digital manufacturing or other easy to replicate methods with full materials and instructions appropriate for communities with different languages and accessibility needs.
Ultimately, it’s about people in the most difficult circumstances getting access to key supplies more quickly than today, so they can recover and rebuild.